Advanced Filtration for Superior Performance
Superfiltration
We believe that excellence in metalworking requires cutting-edge tools and superior filtration quality. That's the reason why Comat has created and developed the concept of superfiltration.
Superfiltration Technology, with a countinuously regenerating filtering media (pre-coat), is the process by which micro- contaminant particles are removed from the cutting fluid while the latter is maintaned at a stable and desired temperature.
The oil filtered with Comat Superfiltration Systems achieves a better cleanliness class than brand new oil (based on ISO and NAS standards, internationally recognized).
Comat Superfiltration systems operate using vegetal or mineral flours, sourced from natural and renewable sources, not dangerous to individuals and non-polluting to the environment. These flours have historically been used in the filtration process of various food and beverage products.
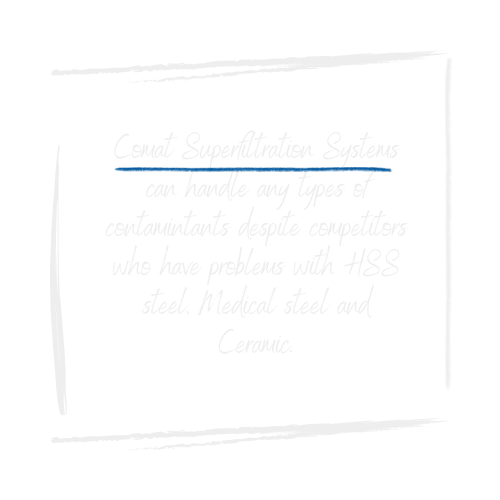
Pre-coat Filtration
ADVANTAGES

EXCELLENT FILTRATION QUALITY

INCREASED OIL LIFESPAN

STABLE FLOW RATE OVER TIME

No limit on oil viscosity

Complete separation between dirty oil tank and clean oil tank

Improved quality and consistency of processed parts

Reduced wear on operating machinery

Production of dry and disposable sludge

Recovery of precious materials

Lower cost for management and maintenance

First-class after-sales service

Industry 4.0 technology
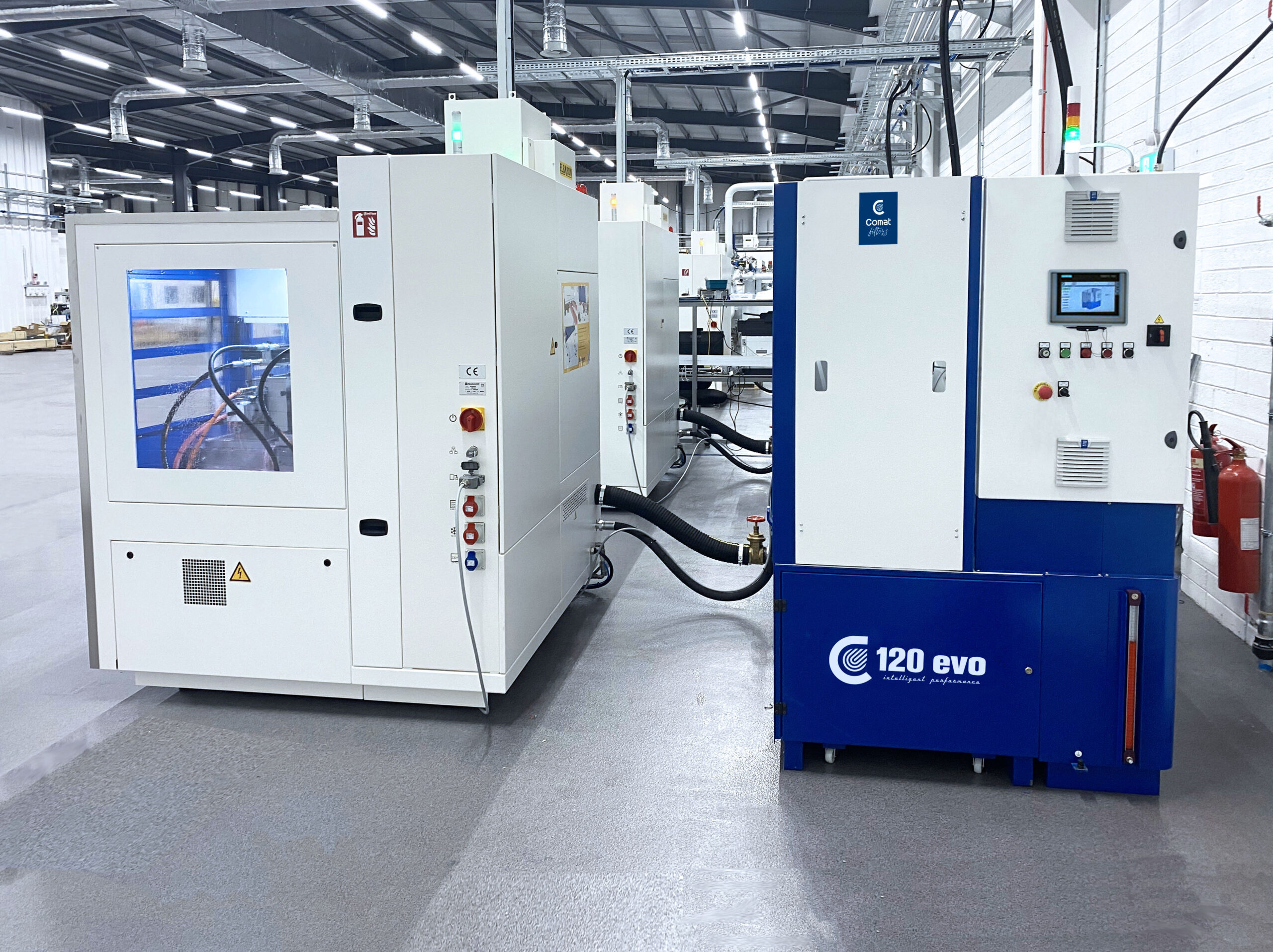
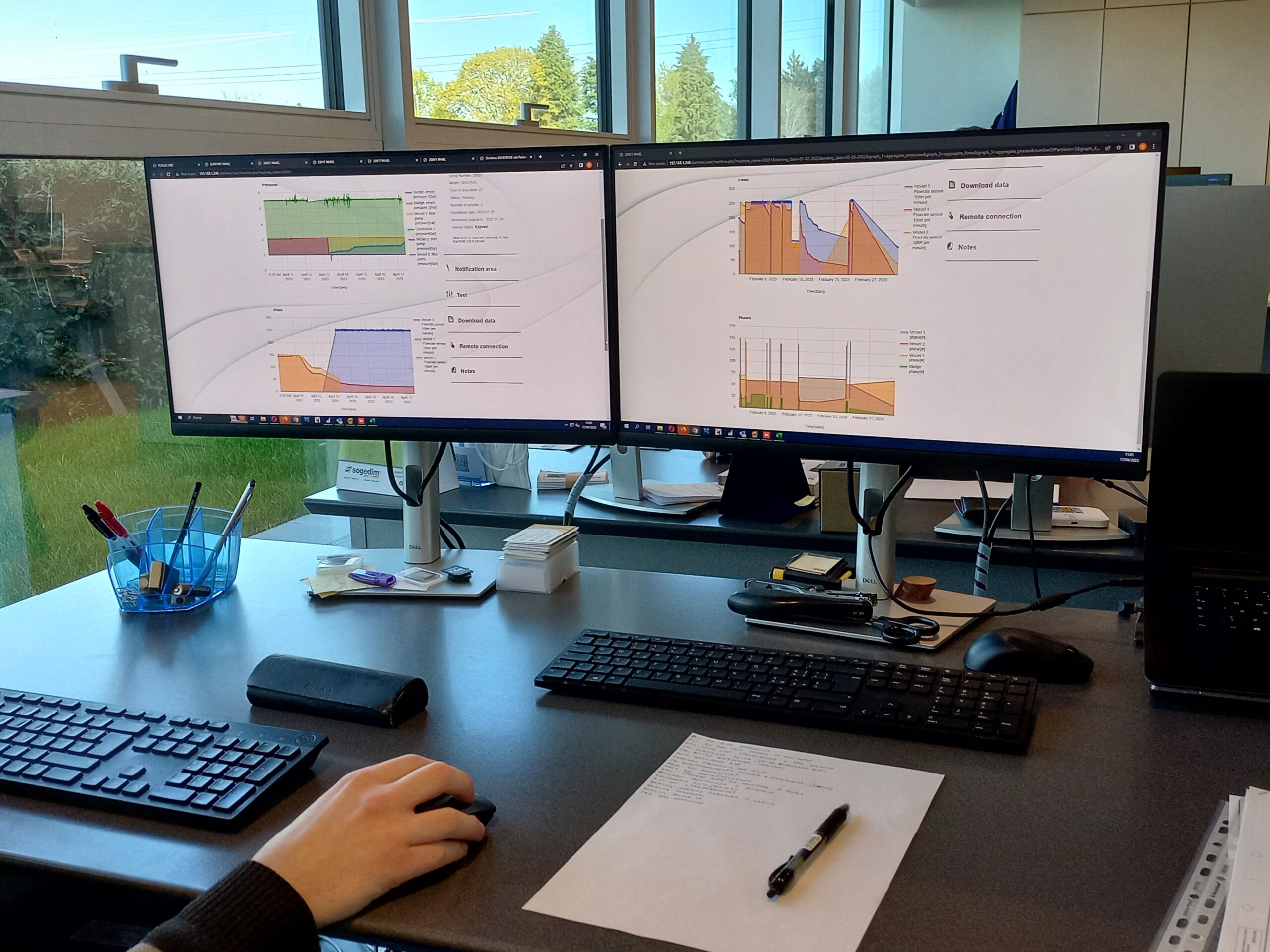
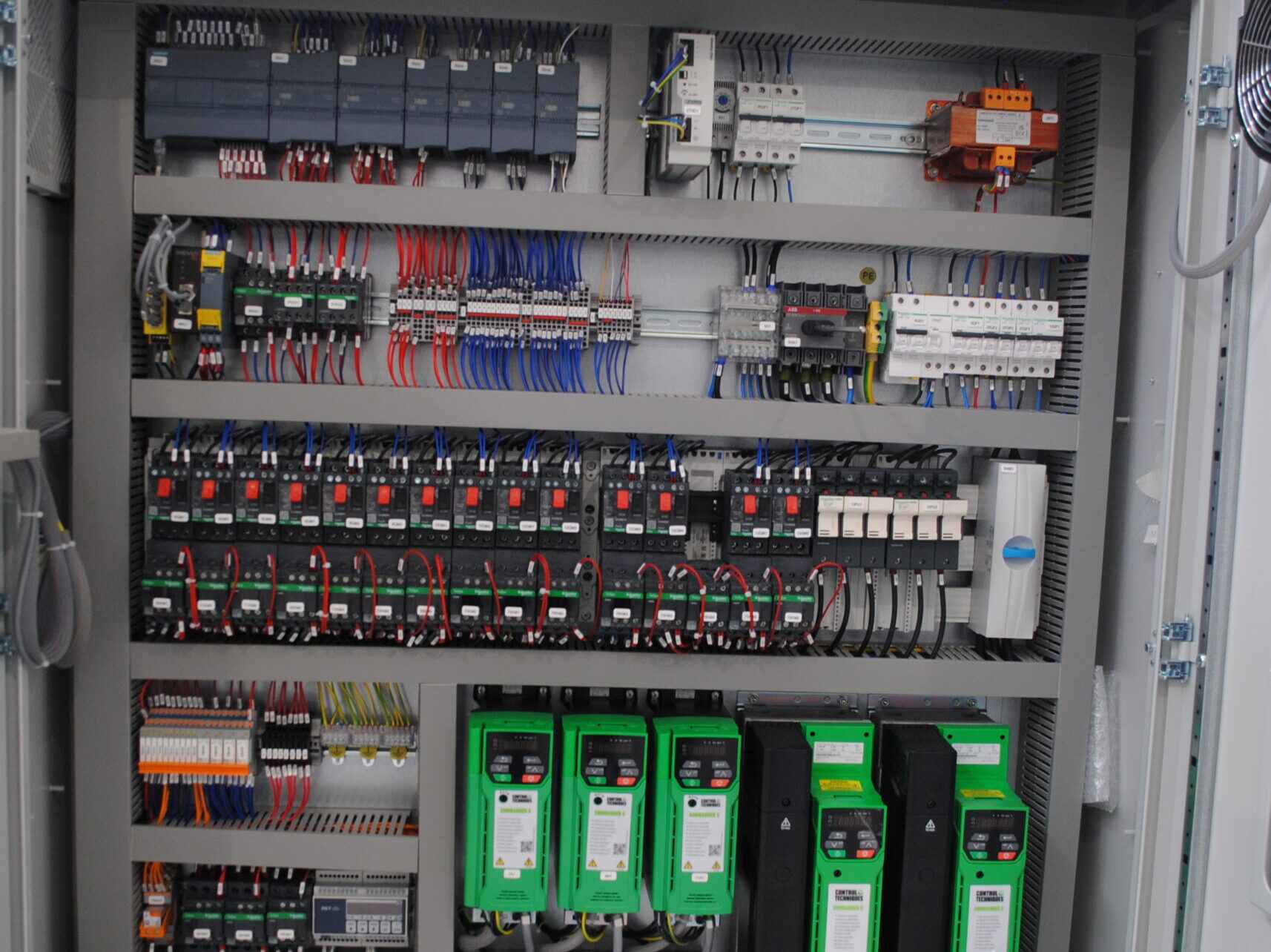
EVO: INTELLIGENT PERFORMANCE
The Comat Superfiltration Systems, in the EVO configuration, represent excellence in the field of filtration thanks to the equippement of "Intelligent Performance Technology".
In the Comat Superfiltration Systems EVO, a processor constantly monitors and adjusts the key parameters of the filtration process, continuously optimizing the system's performance according to effectives production needs.
The Comat EVO filters can be monitored, controlled, and optimized in real-time through the control panel, on-machine management, and even from PC and smartphones.
Precision Machining and Automatic Lathes
APPLICATIONS
The application sector of Superfiltration Technology is mainly dedicated to the surface finishing applications where tolerance and roughness must be strictly controlled to not compromise the quality of the products.
Through the use of Superfiltration Systems, it is possible to achieve an excellent degree of microfiltration of the finest contaminants spread in the working oil and obtain smoother and more precise surfaces, minimizing tool wear and improving their lifespan.
This results in greater precision in machining, reduced waste, and lower maintenance costs, all contributing to an overall increase in productivity.
For this reason, Comat Superfiltration Systems are successfully connected to grinding machines, honing machines, lapping machines, polishing machines and sharpening machines.
Comat Superfiltration Systems are also used in turning applications to filter the oil recovered from chip centrifugation In automatic lathe machining it is customary to use centrifuges to extract oil from the chips.
The centrifuges are also meant to filter the oil, either directly during chips centrifugation or by periodically emptying the lathe tanks. However, oil filtered in this way remains highly contaminated with micro-particles of metal, causing significant wear & tear of the automatic lathes and resulting in unsatisfactory consistency of machined workpieces.
By filtering the oil with one of Comat’s Superfiltration Systems after chip centrifugation, the oil can be brought back to life for an incommensurably better machining and to preserve the performance of your automatic lathes.
OUR PRODUCT RANGE
At Comat, we design and manufacture customized solutions tailored to meet all the specific needs of our customers.
Our product range includes filters for application on individual machines and centralized systems for large production sites.
MODEL
C60
C120
C180
C240
C360
C480
C600
C720
C840
C960
MACHINES MANAGED
1
1
1-2
2
2-3
4-5
5-6
6-8
7-9
8-10
FLOWRATE
60 l/min
120 l/min
180 l/min
240 l/min
360 l/min
480 l/min
600 l/min
720 l/min
840 l/min
960 l/min
MODEL
TM400
TM1000
TM1800
TM3600
TM5400
MACHINES MANAGED
up to 4-5 automatic lathes
up to 8-10 automatic lathes
up to 15-20 automatic lathes
up to 30-40 automatic lathes
up to 50-60 automatic lathes
FLOWRATE
220-430 l/day
480-1000 l/giorno
900-1800 l/day
1800-3600 l/day
3600-5400 l/day
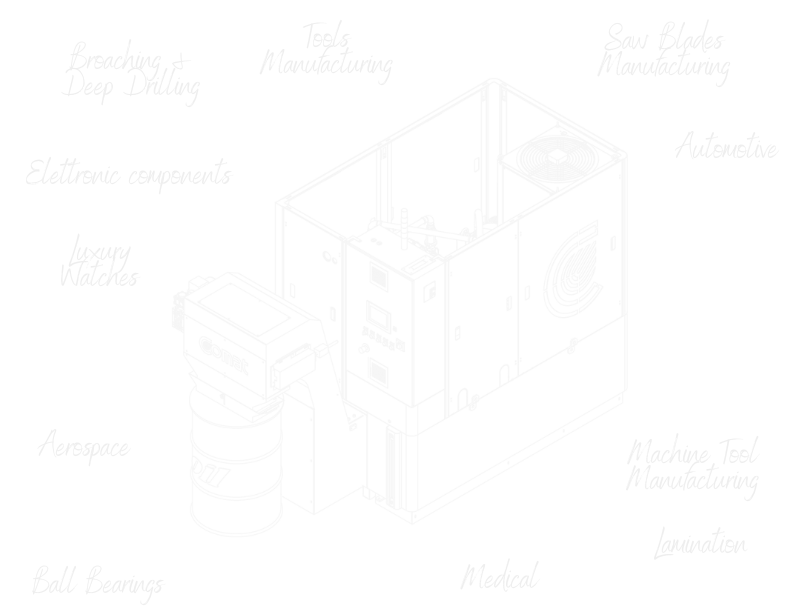